Top 6 Practices For Successful Materials Manufacturing
Manufacturing quality materials is no easy feat. It requires careful planning, strict processes, and a commitment to excellence every step of the way. This guide explores key practices that separate mediocre manufacturers from true masters of their craft.
Meticulous Planning – The Foundation
The old saying rings true – failing to plan is planning to fail. Before firing up a single machine, top manufacturers invest serious time and effort into comprehensive planning and preparation. What materials and quantities are needed? What equipment will be utilized? How should workflows be structured for maximum efficiency? Having clear answers to these types of questions is crucial.
Thorough planning also extends to staffing needs. Who will operate each station? Do workers possess the necessary skills? What training may be required? Overlooking seemingly small personnel details can lead to costly setbacks down the road. Smart manufacturers get the right people in the right roles from day one.
Rigorous Quality Control – Uncompromising Standards
Factories that cut corners inevitably cut quality as well. Manufacturing industry leaders refuse to compromise on quality control in manufacturing processes like custom injection molding at any phase of the manufacturing process. How can this commitment be upheld? Through a multilayered approach involving:
- Strict intake policies for raw and new materials (rejecting substandard components)
- Continuous monitoring of manufacturing conditions like temperatures, moisture levels, etc.
- Random sampling of finished goods for exhaustive examinations, including materials failure analysis
- Efficient communication channels to quickly identify and resolve emerging issues
The mindset is one of proactive prevention rather than reactive damage control. It’s a zero-tolerance policy for defects – period.
Lean Manufacturing – Eliminating Wasteful Practices
In streamlined facilities, every movement, every process, every minute is optimized for maximum productivity. Leaders scrutinize their systems to identify and eliminate any wasteful practices. Is superfluous handling of materials slowing things down unnecessarily? Are workers waiting idly due to an imbalanced workflow? These inefficiencies are red flags for manufacturers embracing lean principles.
Ideal lean environments have minimal downtime, no excess inventory clogging spaces, and finely-tuned logistics that border on perfection. Cross-training personnel is important, too. The more duties someone can handle, the fewer productivity bottlenecks. While challenging to implement, mastering lean practices elevates output and boosts the bottom line.
Cutting-Edge Manufacturing Technology Utilization
As the great Wayne Gretzky said, ‘A good hockey player plays where the puck is. A great hockey player plays where the puck is going to be.’ Leading manufacturers aren’t just utilizing today’s advanced manufacturing technologies – they’re adopting the innovations of tomorrow today.
From advanced robotics for automating repetitive tasks to sophisticated sensors providing granular oversight, tech adoption is vital for accelerating production while maintaining high quality. The Internet of Things (IoT), artificial intelligence (AI), and 3D printing aren’t just buzzwords but game-changing tools that are already being leveraged successfully.
Those scared of new systems risk falling hopelessly behind. The greatest manufacturers aren’t scared at all; they diligently research and implement advances that push their capabilities light years ahead of the competition.
World-Class Talent Acquisition and Retention
Even the fanciest machinery and software are practically useless without the human expertise to operate them properly. Manufacturing leaders know their workforce is their most precious resource, so they aggressively recruit and retain world-class talent at every level.
Beyond technical abilities, these all-star workers possess problem-solving skills, a commitment to continuous progress, and the mental toughness to persevere through difficult periods. Companies woo top talent with generous compensation packages, enticing benefits, robust training, clear pathways for career advancement, and company cultures that reward outstanding performance.
Star players won’t stick around for mediocre opportunities. By rolling out the red carpet, elite manufacturers assemble legendary teams that consistently outperform rivals.
Robust Partner Collaboration
Even with exceptional in-house talent, no manufacturer can succeed entirely alone in today’s interdependent business landscape. Strategic partnerships are force multipliers that give companies access to expansive resources while keeping budgets manageable.
An electronics maker might partner with various component suppliers and logistics providers to diversify its supply chain. A construction company could align with several vendors supplying steel, concrete, lumber, and other building materials. Cooperation is key to guaranteeing seamless access to the goods and services that fuel a manufacturer’s operations.
The best partnerships transcend basic transactions; they’re bonded by shared visions and mutual respect. Both sides proactively communicate and collaboratively solve issues in a spirit of teamwork. Manufacturers who’ve cultivated a network of reliable partners can better weather disruptions and thrive over the competition.
Final Thoughts
By internalizing and applying these practices, today’s facilities can manufacture tomorrow’s greatest successes. It all begins with commitment and continuous improvement. Those who embrace the principles of manufacturing mastery will be richly rewarded by superior productivity, quality, and profits. The choice, as always, is yours.
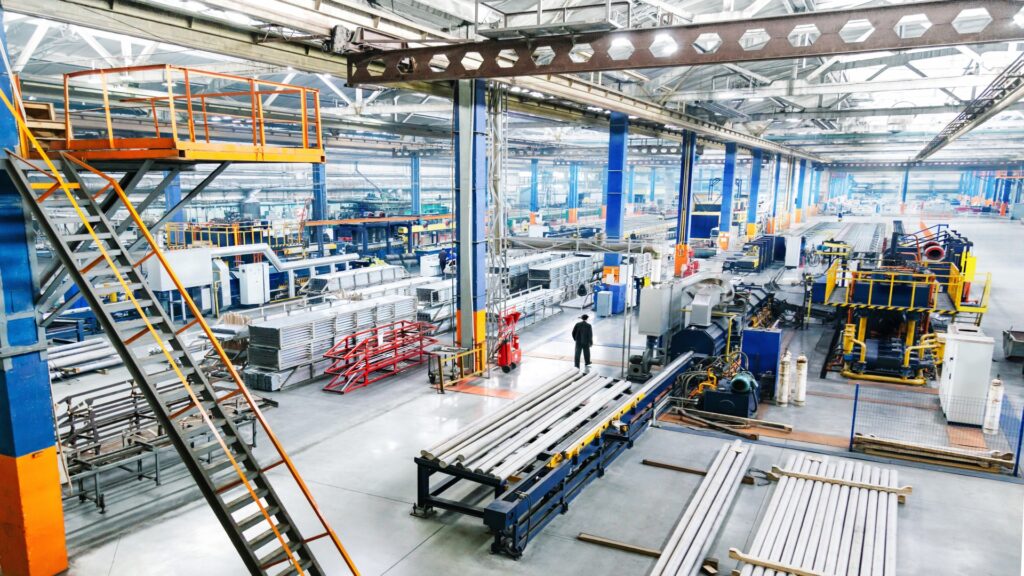